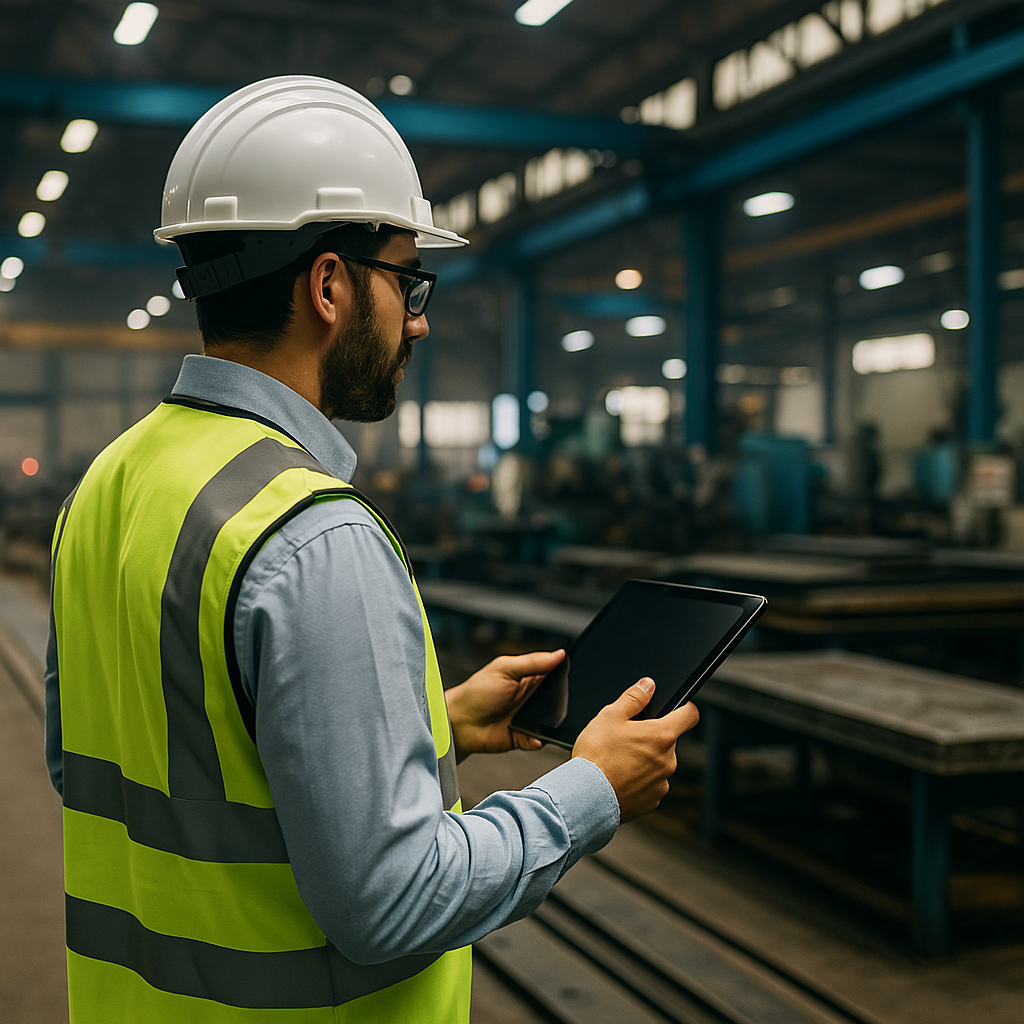
Comment Augmenter la Capacité de Production et Maximiser la Fabrication
Introduction
Dans un marché manufacturier en constante évolution, augmenter la capacité de production est un levier clé pour répondre à la demande croissante et améliorer la rentabilité. La capacité de production détermine la quantité maximale de produits qu’une usine peut fabriquer sur une période donnée, en fonction de ses machines-outils, de sa main-d’œuvre et de son organisation. L’optimisation de cette capacité passe par une meilleure planification de la production, une gestion efficace des temps de cycle, et l’intégration de solutions technologiques avancées comme les logiciels de suivi des machines.
Cet article explore plusieurs stratégies pour maximiser la production sans compromettre la qualité ni augmenter excessivement les coûts.
Analyser la Capacité Actuelle de Production
Avant de chercher à augmenter la capacité de production, il est crucial d’analyser la situation actuelle. Un logiciel de suivi des machines permet d’identifier les goulets d’étranglement et d’analyser les performances des équipements en temps réel.
La surveillance en temps réel des temps de cycle, des temps d’arrêt et de l’efficacité globale des équipements fournit des données essentielles pour optimiser les processus. Un bon point de départ est d’évaluer le TRS (Taux de Rendement Synthétique), qui mesure l’efficacité de la production en prenant en compte la disponibilité, la performance et la qualité.
Optimiser l’Utilisation des Machines-Outils
Les machines-outils jouent un rôle clé dans la capacité de production. Un logiciel de suivi de la production permet d’optimiser leur utilisation en identifiant les périodes d’inactivité et en réduisant les temps morts.
L’automatisation des processus avec des programmes CN permet également d’améliorer la productivité en réduisant les erreurs humaines et en optimisant les temps d’usinage. Un programme de production bien structuré assure une transition fluide entre les différentes tâches et améliore l’efficacité globale.
Réduire les Temps de Changement
Les temps de changement de série sont une source majeure de ralentissement de la production. En appliquant la méthode SMED (Single-Minute Exchange of Die), il est possible de réduire considérablement le temps nécessaire pour passer d’un produit à un autre.
L’optimisation des processus de changement passe par la standardisation des tâches, l’automatisation des réglages et l’amélioration de la coordination entre les opérateurs et les logiciels de planification des effectifs. Cela permet d’augmenter la flexibilité de la production et de maximiser le rendement des machines.
Mettre en Place un Logiciel de Planification de la Production
Une planification efficace est essentielle pour maximiser la capacité de production. L’utilisation d’un logiciel de planification de la production permet de coordonner l’utilisation des équipements, des matières premières et de la main-d’œuvre de manière optimale.
La planification en direct permet de s’adapter rapidement aux fluctuations de la demande et d’éviter les interruptions inutiles. Un logiciel de planification des effectifs assure une répartition intelligente des ressources humaines, en tenant compte des compétences disponibles et des besoins spécifiques de la production.
Automatiser et Numériser les Processus
L’automatisation industrielle est un levier puissant pour augmenter la capacité de production. L’intégration de robots industriels, de machines-outils connectées et de logiciels de suivi des programmes CN permet de réduire la dépendance aux interventions manuelles et d’optimiser les cycles de production.
Les solutions de surveillance en temps réel et de suivi des temps d’arrêt facilitent la détection des inefficacités et permettent d’apporter des ajustements immédiats. L’objectif est d’accélérer la cadence sans compromettre la qualité.
Améliorer la Gestion de la Main-d’Œuvre
Une gestion efficace des effectifs est essentielle pour éviter les pertes de temps et optimiser la production. Un logiciel de planification des effectifs permet d’attribuer les tâches de manière stratégique, en fonction des compétences et de la charge de travail.
Former continuellement les opérateurs à l’utilisation des nouvelles technologies et des programmes CN permet également d’améliorer l’efficacité. Une planification en direct permet d’anticiper les besoins en personnel et d’assurer une flexibilité optimale.
Réduire les Gaspillages et Améliorer la Qualité
Les défauts de fabrication, les rebuts et les reprises augmentent le temps nécessaire pour produire une unité. En mettant en place un système de surveillance en temps réel, il est possible d’identifier rapidement les sources de gaspillage et d’améliorer les processus de contrôle qualité.
L’adoption de méthodes comme le Lean Manufacturing et le Six Sigma aide à éliminer les inefficacités et à standardiser les processus de production pour garantir une meilleure rentabilité.
Étude de Cas : Augmentation de la Capacité de Production dans un Atelier d’Usinage
Prenons l’exemple d’une entreprise spécialisée dans la fabrication de composants mécaniques. Avant l’optimisation, la production était limitée par des temps de cycle élevés et des interruptions fréquentes.
Après l’intégration d’un logiciel de suivi des machines, d’un programme de production optimisé et de robots d’assistance à l’usinage, l’entreprise a pu :
- Augmenter sa capacité de production de 25 % en réduisant les pertes de temps.
- Réduire les temps d’arrêt de 40 % grâce à un suivi en temps réel et une maintenance préventive.
- Optimiser l’utilisation de ses machines-outils en adaptant les programmes CN aux performances réelles des équipements.
Grâce à ces améliorations, l’entreprise a pu répondre plus rapidement aux commandes clients tout en réduisant ses coûts de fabrication.
Conclusion
Augmenter la capacité de production ne signifie pas uniquement ajouter de nouvelles machines ou embaucher plus de personnel. Une approche stratégique basée sur l’optimisation des ressources existantes permet d’obtenir des résultats significatifs.
L’utilisation de logiciels de suivi des machines, de planification de la production et d’automatisation avancée offre des solutions concrètes pour maximiser le rendement. En combinant la suivi en temps réel, planification des effectifs et gestion optimisée des temps de cycle, les fabricants peuvent améliorer leur compétitivité tout en garantissant une production plus efficace et flexible.
En appliquant ces stratégies, les entreprises peuvent non seulement augmenter leur capacité de production, mais aussi améliorer leur qualité et réduire leurs coûts d’exploitation, assurant ainsi une meilleure rentabilité sur le long terme.