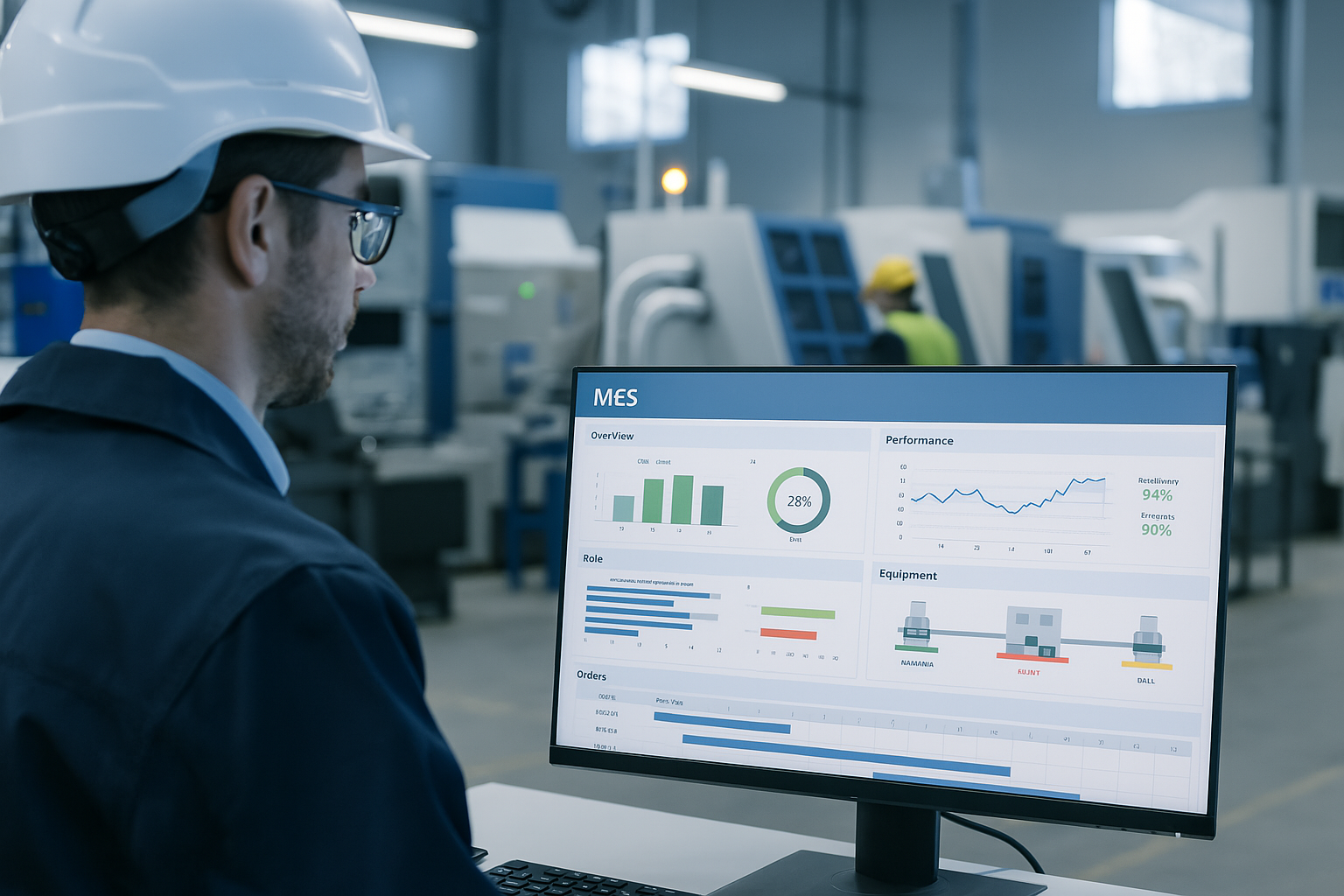
Guide Définitif sur les Systèmes d’Exécution de la Fabrication (MES)
Introduction
Dans un environnement de production de plus en plus automatisé et connecté, les systèmes d’exécution de la fabrication (MES - Manufacturing Execution Systems) jouent un rôle essentiel dans l’optimisation des processus industriels. Un MES permet d’assurer une meilleure planification de la production, d’améliorer le Taux de Rendement Synthétique (TRS) et d’intégrer les machines-outils à un système centralisé de gestion des opérations.
Cet article explore en détail le rôle des MES, leur fonctionnement, leurs avantages et leur impact sur l’efficacité globale des équipements.
Qu’est-ce qu’un Système d’Exécution de la Fabrication (MES)?
Un MES (Manufacturing Execution System) est un logiciel industriel qui suit et contrôle la production en temps réel. Il se situe entre les systèmes de gestion ERP (Enterprise Resource Planning) et les machines-outils, assurant ainsi une communication fluide entre la planification stratégique et l’atelier.
Le MES permet d’analyser les temps de cycle, d’optimiser les programmes CN, de suivre la suivi en temps réel des machines et d’améliorer la planification des effectifs.
Fonctionnalités Clés d’un Système MES
Un MES comprend plusieurs fonctionnalités essentielles pour améliorer la gestion de la production:
- Suivi en temps réel des machines-outils : Permet d’identifier immédiatement les pannes et les ralentissements.
- Gestion des ordres de fabrication: Coordonne les programmes de production et assure une traçabilité complète.
- Optimisation des temps de cycle : Ajuste automatiquement les paramètres pour améliorer l’efficacité.
- Suivi des performances et des indicateurs de production : Analyse l’efficacité globale des équipements (OEE) et les temps d’arrêt.
- Gestion de la qualité et des défauts: Réduit le nombre de rebuts et optimise la production.
- Planification des effectifs et allocation des tâches : Assure une meilleure utilisation des ressources humaines et matérielles.
Pourquoi un MES est-il Essentiel dans l’Industrie 4.0?
Dans un contexte d’usine intelligente, les MES sont devenus incontournables pour maximiser l’utilisation des machines-outils et garantir une production fluide. Voici leurs principaux avantages:
1. Amélioration de la Planification de la Production
Un MES aide à coordonner les opérations, en intégrant la planification en direct et en optimisant l’affectation des ressources.
2. Optimisation des Temps de Cycle et des Changements de Série
Les temps de changement de série et les temps de cycle sont optimisés grâce à une analyse en temps réel des performances des machines-outils.
3. Réduction des Temps d’Arrêt et des Pertes
Un MES permet d’identifier rapidement les causes des temps d’arrêt et d’implémenter des stratégies correctives.
4. Meilleure Gestion des Effectifs
Grâce à un logiciel de planification des effectifs, le MES garantit une meilleure allocation des opérateurs et réduit les périodes d’inactivité.
5. Automatisation et Intégration des Données
Un MES permet d’intégrer plusieurs outils et logiciels industriels (ERP, SCADA, logiciels de suivi des machines), réduisant ainsi les erreurs et améliorant l’analyse des performances.
MES vs. ERP vs. SCADA : Quelle Différence?
Système |
Rôle Principal |
Portée |
ERP (Enterprise Resource Planning) |
Planification stratégique et gestion des ressources |
Niveau global de l’entreprise |
MES (Manufacturing Execution System) |
Suivi et contrôle en temps réel de la production |
Niveau atelier |
SCADA (Supervisory Control and Data Acquisition) |
Supervision et contrôle des équipements industriels |
Niveau opérationnel |
Un MES agit donc comme un pont entre l’ERP et le SCADA, assurant une coordination efficace des opérations industrielles.
Mise en Place d’un Système MES
L’implémentation d’un MES nécessite une approche structurée pour garantir son efficacité. Voici les principales étapes:
1. Définir les Objectifs et les Besoins
Avant d’intégrer un MES, il est essentiel d’identifier les problèmes de production existants et les objectifs à atteindre (réduction des temps de cycle, amélioration du TRS, optimisation des programmes CN).
2. Sélectionner un MES Adapté
Il existe plusieurs solutions de MES, certaines étant plus adaptées aux petites entreprises, tandis que d’autres conviennent aux grandes industries manufacturières. Les critères de sélection incluent:
- Intégration avec les logiciels de planification de la production et ERP existants.
- Compatibilité avec les machines-outils et les équipements industriels.
- Facilité d’utilisation et formation des opérateurs.
3. Automatiser le Suivi des Performances
L’intégration d’un logiciel de suivi des machines permet d’obtenir des données précises sur les temps d’arrêt, les temps de cycle et l’efficacité globale des équipements.
4. Former les Opérateurs et Responsables de Production
L’adoption d’un MES nécessite une formation approfondie des équipes pour garantir son utilisation optimale et maximiser son impact sur la planification des effectifs.
5. Surveiller et Améliorer en Continu
Une fois le MES en place, il est important d’analyser régulièrement les performances et d’ajuster les paramètres pour optimiser la production.
Cas d’Utilisation: Amélioration de la Production avec un MES
Une entreprise spécialisée dans l’usinage de précision souhaitait améliorer sa productivité et réduire les pertes. Après l’implémentation d’un MES, elle a pu:
- Augmenter son TRS de 20 % grâce à une meilleure gestion des temps de cycle.
- Réduire ses temps de changement de série de 35 % en optimisant la planification.
- Diminuer les rebuts de production de 25 % en améliorant le suivi de la qualité.
Grâce à ces améliorations, l’entreprise a pu optimiser sa planification de la production, réduire ses coûts et améliorer sa compétitivité.
Conclusion
Un Manufacturing Execution System (MES) est un outil indispensable pour les fabricants souhaitant améliorer leur efficacité globale des équipements, réduire les temps d’arrêt et optimiser leurs programmes CN. Il joue un rôle clé dans l’intégration des machines-outils, la gestion des effectifs et l’optimisation des temps de cycle.
L’adoption d’un MES, combinée à l’utilisation de logiciels de suivi des machines et d’outils de planification de la production, permet aux industriels d’accélérer leur transition vers l’industrie 4.0, garantissant ainsi une production plus efficace, flexible et compétitive.