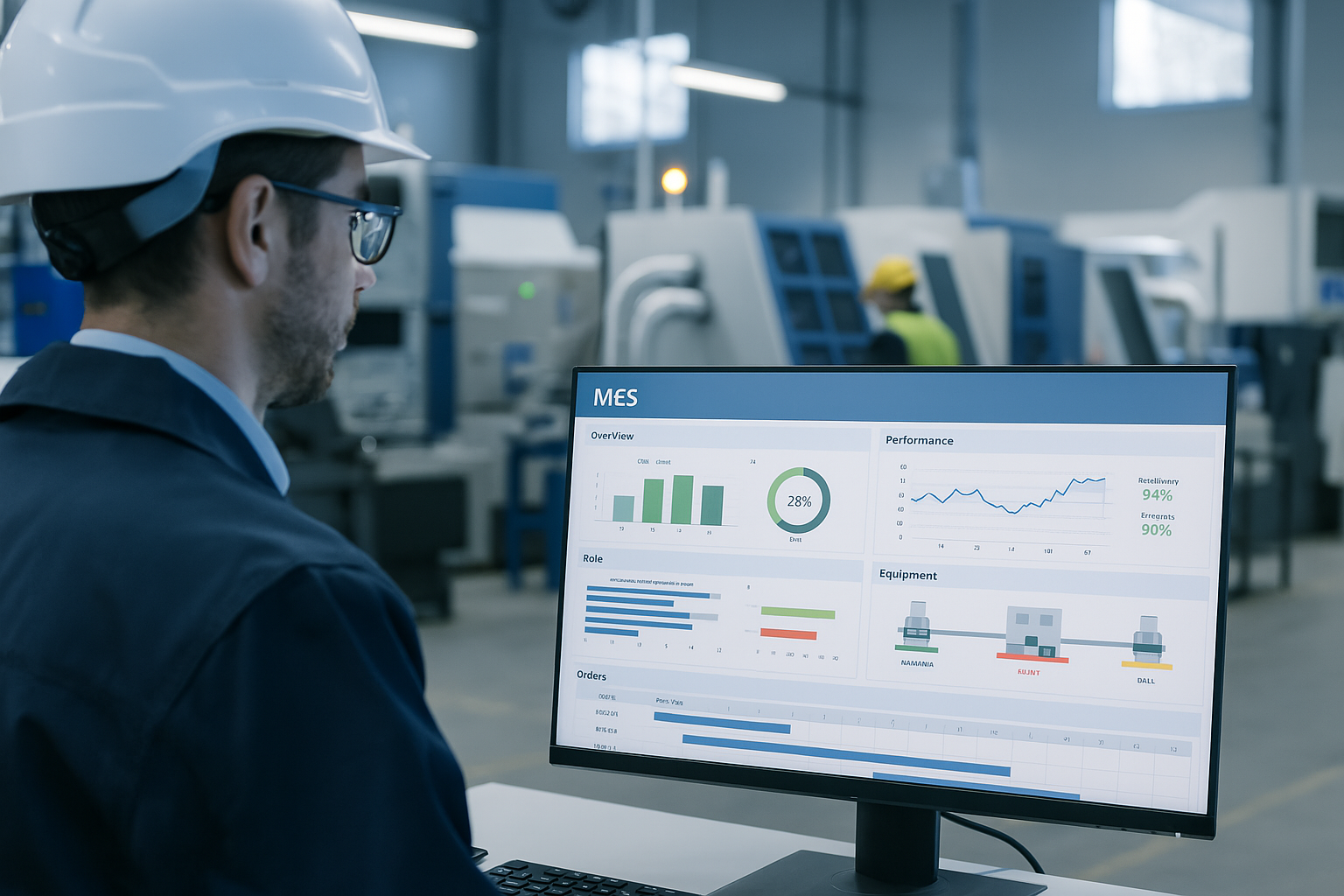
Definitive Guide to Manufacturing Execution Systems (MES)
Introduction
In an increasingly automated and connected production environment, Manufacturing Execution Systems (MES) play a vital role in optimizing industrial processes. An MES enables better production planning, improves Overall Equipment Effectiveness (OEE), and integrates CNC machines into a centralized operations management system.
This article explores in detail what MES systems are, how they work, their benefits, and their impact on production efficiency.
What is a Manufacturing Execution System (MES)?
An MES is an industrial software that monitors and controls production in real time. It acts as a bridge between ERP (Enterprise Resource Planning) systems and CNC machines, enabling smooth communication between strategic planning and shop floor operations.
MES software supports cycle time analysis, CNC program optimization, real-time machine monitoring, and improved workforce planning.
Key Features of an MES
An MES includes several essential features that improve production management:
-
-
Real-time machine monitoring: Detects downtimes and slowdowns instantly.
-
Work order management: Coordinates production orders and ensures full traceability.
-
Cycle time optimization: Automatically adjusts parameters to improve efficiency.
-
Production performance tracking: Analyzes OEE and machine downtime.
-
Quality and defect tracking: Reduces scrap rates and optimizes output.
-
Workforce planning and task allocation: Improves the use of human and material resources.
-
Why Is MES Essential in Industry 4.0?
In a smart factory context, MES has become indispensable to maximize machine utilization and ensure smooth production flow. Key advantages include:
1. Improved Production Planning
MES helps coordinate operations through live scheduling and resource optimization.
2. Optimized Cycle Times and Changeovers
Cycle times and changeover durations are optimized through real-time machine performance analysis.
3. Reduced Downtime and Losses
MES quickly identifies root causes of downtime and enables corrective action.
4. Better Workforce Management
With integrated workforce planning, MES ensures optimal operator allocation and minimizes idle time.
5. Automation and Data Integration
MES connects various industrial systems (ERP, SCADA, machine monitoring software), reducing errors and improving performance analytics.
MES vs. ERP vs. SCADA: What’s the Difference?
System | Main Role | Scope |
---|---|---|
ERP (Enterprise Resource Planning) | Strategic planning and resource management | Enterprise-wide |
MES (Manufacturing Execution System) | Real-time production monitoring and control | Shop floor level |
SCADA (Supervisory Control and Data Acquisition) | Equipment-level control and supervision | Operational level |
MES serves as the link between ERP and SCADA, enabling coordinated industrial execution.
How to Implement an MES
A structured approach is required to ensure MES effectiveness. Here are the key steps:
1. Define Goals and Needs
Before implementation, identify existing production issues and objectives (e.g., reduce cycle time, improve OEE, optimize CNC programs).
2. Choose the Right MES
Different MES solutions exist. Some fit small shops, others serve large-scale manufacturers. Key selection criteria:
-
Integration with existing ERP and planning tools
-
Compatibility with CNC machines and industrial equipment
-
Ease of use and operator training
3. Automate Performance Monitoring
Linking MES with a machine monitoring system provides accurate data on downtime, cycle time, and OEE.
4. Train Operators and Production Leaders
Successful adoption requires in-depth training to ensure optimal use and workforce planning benefits.
5. Monitor and Continuously Improve
Once deployed, analyze results regularly and fine-tune settings to optimize production.
Use Case: Boosting Production with MES
A precision machining company aimed to boost productivity and reduce losses. After implementing an MES, they:
-
Increased OEE by 20% via better cycle time control
-
Reduced changeover time by 35% through improved scheduling
-
Lowered scrap rates by 25% with enhanced quality tracking
These improvements helped optimize production planning, lower costs, and increase competitiveness.
Conclusion
A Manufacturing Execution System (MES) is essential for manufacturers aiming to improve OEE, reduce downtime, and optimize CNC operations. It plays a key role in integrating machines, managing workforce, and streamlining cycle times.
Adopting an MES alongside machine monitoring systems and production planning software supports the shift toward Industry 4.0 and enables a more efficient, agile, and competitive production environment.