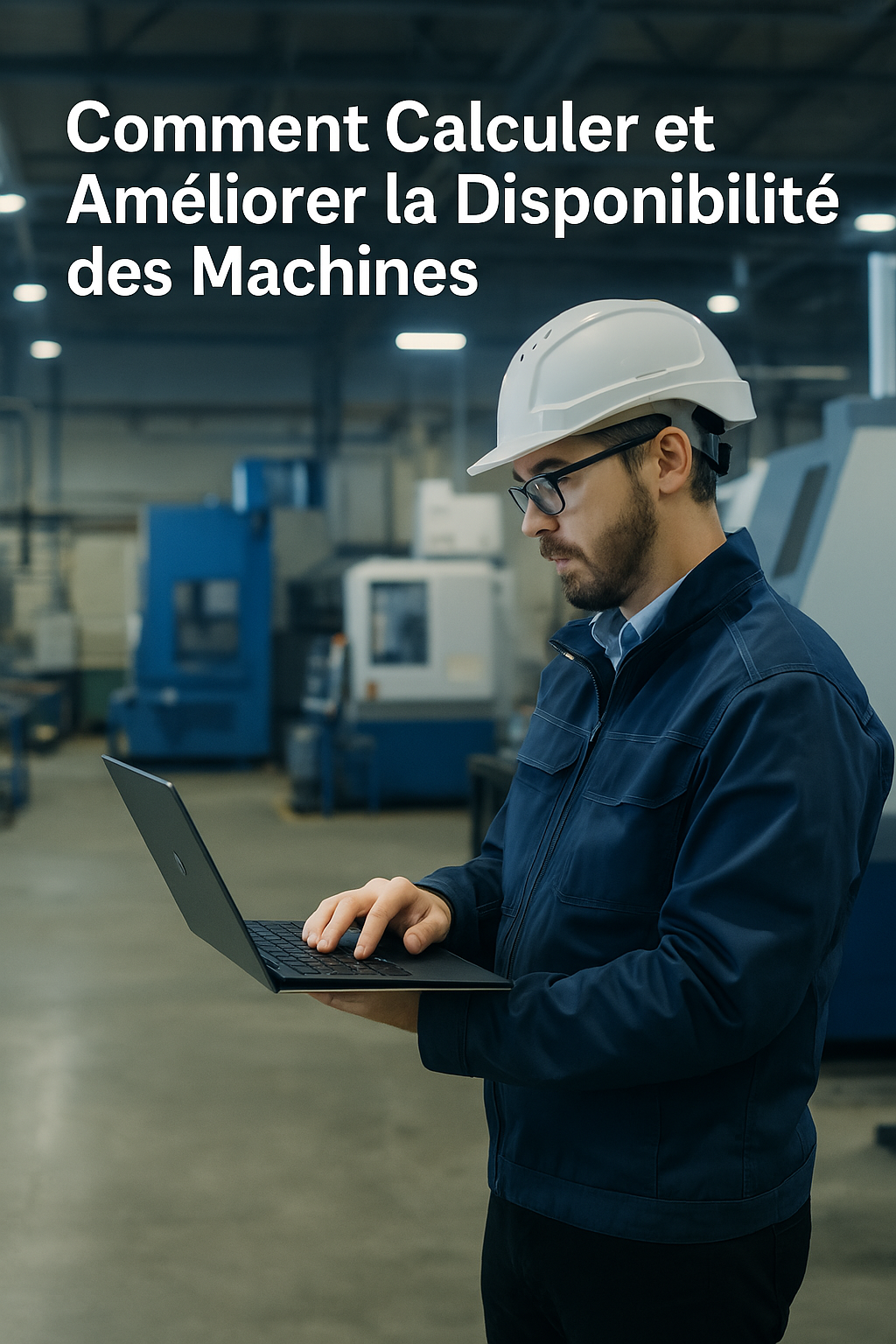
How to Calculate and Improve Machine Availability
Introduction
Machine availability is a key performance indicator in the manufacturing industry. It measures the proportion of time a machine tool is operational compared to the total time it is scheduled to be. Low availability results in production interruptions, lower productivity, and higher costs. On the other hand, optimizing machine availability improves OEE (Overall Equipment Effectiveness), increases production capacity, and minimizes losses.
This article explores how to calculate and improve machine availability using solutions such as real-time machine monitoring, preventive maintenance, and cycle time and downtime optimization.
What is Machine Availability?
Machine availability is part of overall equipment effectiveness. It represents the percentage of time a machine tool is functioning compared to its scheduled production time. Several factors affect it, including unplanned downtime, changeover times, and maintenance quality.
How to Calculate Machine Availability
Machine availability is calculated with the following formula:
Availability (%) = (Operating Time / Planned Production Time) × 100
For example, if a machine is scheduled to run for 10 hours a day but breaks down for 2 hours, its operating time is 8 hours.
An availability rate of 80% means that the machine tool is operational for 80% of its scheduled time. The goal is to increase this percentage to maximize production planning and reduce losses.
Factors Affecting Machine Availability
1. Unplanned Downtime
Unexpected failures are one of the main causes of lost availability. These are often due to a lack of CNC program monitoring, component wear, or human error. Real-time tracking of downtime helps identify recurring issues and implement improvement strategies.
2. Changeover Times
Changeover times can slow down production and reduce machine availability. Applying the SMED (Single-Minute Exchange of Die) method helps optimize these transitions and minimize lost time between runs.
3. Poorly Planned Maintenance
Unoptimized maintenance can cause frequent breakdowns and poor resource management. Implementing a preventive maintenance plan and using a machine monitoring system help anticipate needs and avoid unnecessary interruptions.
4. Poor Resource Management
Inefficient workforce planning can delay maintenance actions and machine operation. A production planning system ensures better task allocation and smoother resource management.
Strategies to Improve Machine Availability
1. Implement a Machine Monitoring System
A machine monitoring system provides real-time performance data. It delivers accurate insights into OEE, downtimes, and cycle times, helping identify inefficiencies and apply corrective actions.
2. Optimize Maintenance with a Preventive Plan
Rather than waiting for breakdowns, preventive maintenance based on machine data analysis allows planned interventions before issues occur. This reduces unexpected failures and extends equipment life.
3. Improve Production Planning
A production planning system coordinates operations and optimizes machine use. With live scheduling, it’s possible to quickly adjust plans to minimize downtime and maximize output.
4. Automate Processes and Reduce Human Errors
Automation and CNC programming optimize processes and reduce manual errors. Fewer errors mean fewer breakdowns and smoother production continuity.
5. Reduce Changeover Times
The SMED method helps structure and standardize changeover steps to minimize interruptions. By reducing transition times, machine tools remain operational longer.
6. Track and Analyze Production Data
A production monitoring system collects and analyzes real-time data to identify problems and enhance machine tool management. With detailed reports on cycle times, downtime, and overall equipment efficiency, continuous optimization of machine availability is possible.
Case Study: Improving Machine Availability
A mechanical parts manufacturer was experiencing frequent downtime, limiting its production capacity. After implementing a machine monitoring system and a preventive maintenance program, the company:
-
Increased machine availability from 75% to 92% by reducing unplanned failures.
-
Reduced changeover times by 40% through the SMED method.
-
Optimized workforce planning for faster maintenance interventions.
These improvements boosted OEE, reduced operating costs, and increased productivity.
Conclusion
Machine availability is crucial for improving production planning and maximizing profitability. By implementing strategies such as real-time monitoring, preventive maintenance, and optimizing cycle times, it's possible to significantly increase machine tool availability.
Using a machine monitoring system, a production planning system, and structured workforce planning enables manufacturers to reduce interruptions and ensure efficient, uninterrupted production.