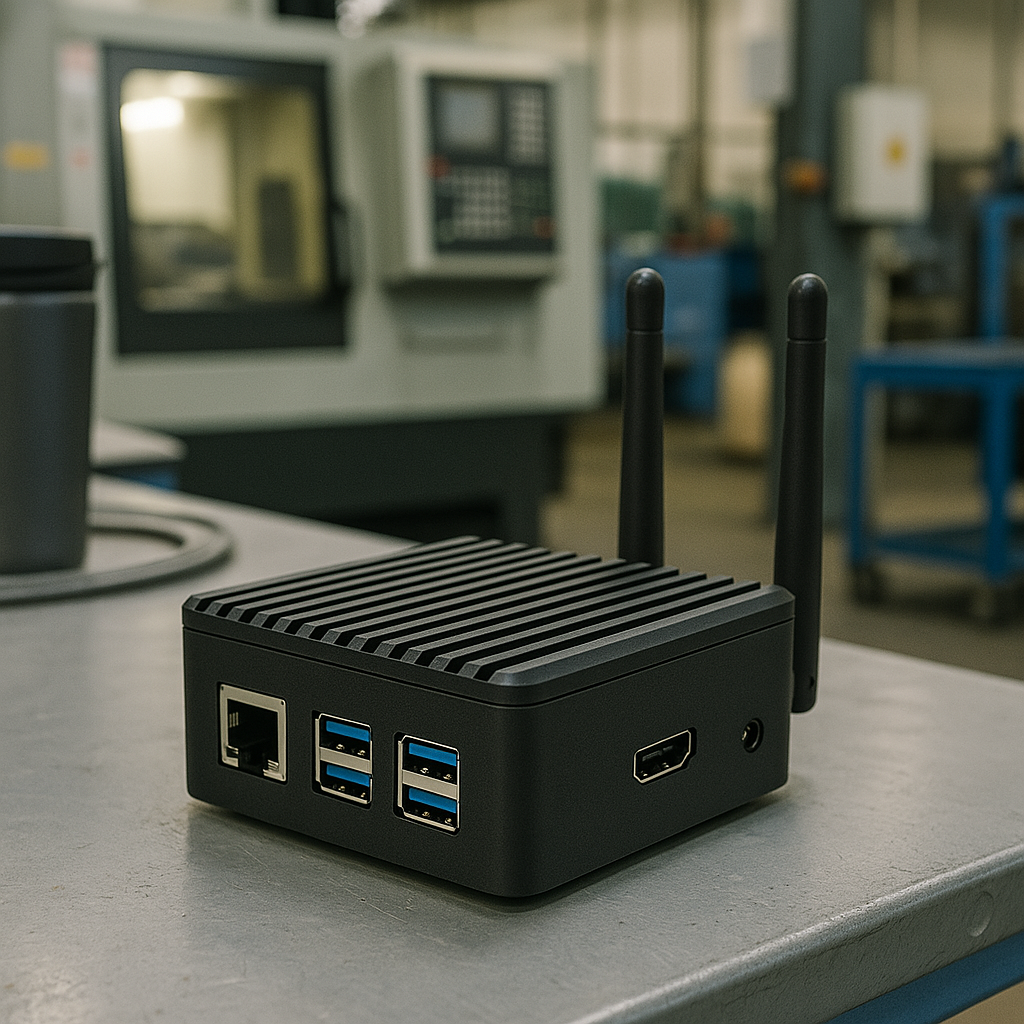
What is an Edge Device and Why Is It Essential for IoT?
Introduction
The Internet of Things (IoT) is transforming the industry by connecting machines and sensors to intelligent networks capable of processing and analyzing data in real time. At the heart of this revolution are Edge Devices — strategic equipment that enhances communication, optimizes real-time monitoring, and improves the efficiency of CNC machines.
Edge Devices are essential for managing and processing data locally before sending it to the cloud, thereby reducing latency and improving decision-making speed. This article explores the role of Edge Devices, their benefits, and their impact on production planning and the optimization of industrial performance.
What is an Edge Device and Why Is It Essential for IoT?
An Edge Device is a computing hardware located between CNC machines and the network infrastructure (cloud, data centers, or other servers). Its main role is to collect, process, and transmit production data in real time, enabling more efficient management of industrial operations.
Edge Devices come in various forms:
-
-
Smart sensors: Measure temperature, pressure, or humidity.
-
IoT gateways: Ensure communication between equipment and IT networks.
-
Industrial controllers: Manage automation and production processes.
-
Why Are Edge Devices Essential for Industrial IoT?
In the manufacturing industry, Edge Devices enhance productivity and reduce inefficiencies by optimizing machine management and facilitating production planning. Here are their main advantages:
1. Reduced Latency and Increased Responsiveness
Edge Devices process data locally, avoiding the need to constantly send information to the cloud. This reduces latency and allows machine monitoring software to respond immediately in the event of a problem.
For example, if a sensor detects that a CNC machine is overheating, the Edge Device can trigger a signal to stop production or initiate maintenance without waiting for a response from a remote server.
2. Improved Reliability and Security
By processing data locally, Edge Devices minimize the transmission of sensitive information over the network, thereby reducing cybersecurity risks. They also enable machine monitoring software to function even if the cloud connection is temporarily lost.
3. Optimized Cycle Times and Performance Tracking
Integrating Edge Devices with machine monitoring software enables advanced analysis of cycle times, equipment performance, and CNC program efficiency. Real-time data is essential for improving Overall Equipment Effectiveness (OEE) and reducing changeover times.
4. Better Resource Management and Production Planning
Thanks to Edge Computing, manufacturers can better manage production programs by adjusting schedules based on actual machine performance. A production planning software connected to Edge Devices helps optimize task distribution and workforce management.
Key Features of Edge Devices in Industry
A high-performance Edge Device should include several features to ensure effective integration with CNC machines and CNC program monitoring software:
-
Real-time data collection and processing
-
Equipment performance monitoring
-
Secure communication with cloud systems and databases
-
Automation of maintenance and production processes
-
Integration with workforce and production planning software
Integrating Edge Devices with Industrial IoT
Edge Computing complements the cloud, offering a balance between local storage and centralized data management. Here's how Edge Devices fit into industrial IoT:
-
Data Collection: Sensors connected to CNC machines continuously send data to Edge Devices.
-
Local Processing: The Edge Device analyzes cycle times, detects anomalies, and optimizes machine usage.
-
Selective Data Transmission: Only critical data is sent to the cloud, reducing network load.
-
Enhanced Preventive Maintenance: Edge Computing helps detect potential failures before they occur, making production planning and workforce management more effective.
Use Cases of Edge Devices in Manufacturing
1. Real-Time CNC Machine Monitoring
A precision machining company integrated Edge Devices to monitor equipment status in real time. The result: a 30% reduction in unplanned downtime and improved preventive maintenance thanks to more accurate data.
2. Cycle Time Optimization
In an automotive production facility, Edge Devices were used to analyze cycle times and adjust CNC programs based on actual equipment performance. This led to a 20% increase in productivity.
3. Reduced Maintenance Costs
An industrial equipment manufacturer deployed Edge Devices to monitor wear on critical components and adjust production programs accordingly. Thanks to better task planning, maintenance costs were reduced by 25%.
Conclusion
Edge Devices are key components of Industrial IoT, enabling real-time monitoring, optimized CNC machine management, and improved production planning. By processing data locally, they ensure faster responsiveness, reduce latency, and strengthen cybersecurity.
The adoption of machine monitoring and workforce planning software integrated with Edge Devices offers a competitive advantage for manufacturers aiming to optimize production and improve their Overall Equipment Effectiveness (OEE). Industry 4.0 relies on these technologies to deliver smarter, more flexible, and more efficient production.