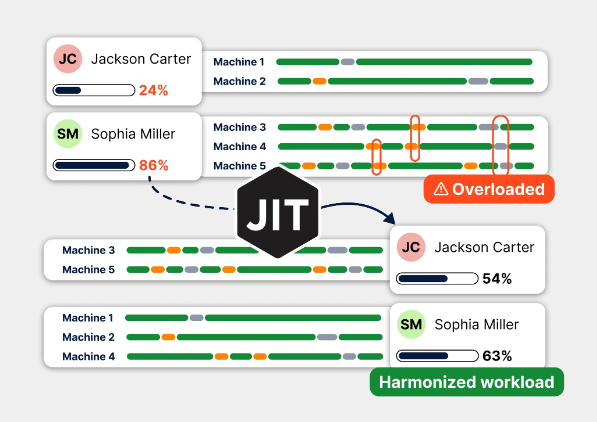
Overcoming Labor Shortage: Know Your Operators' Workload
Key Takeaways:
- Labor shortage: The labor shortage is preventing the manufacturing industry from running at full capacity, creating delay in the supply chain.
- Understanding Operator Workload: Recognizing the full scope of operators' tasks and their workload is crucial for optimizing the use of available resources.
- Improving Machine-to-Operator Ratio: With better insight into workloads, it's possible to intelligently assign multiple machines to operators without overburdening them, enhancing productivity.
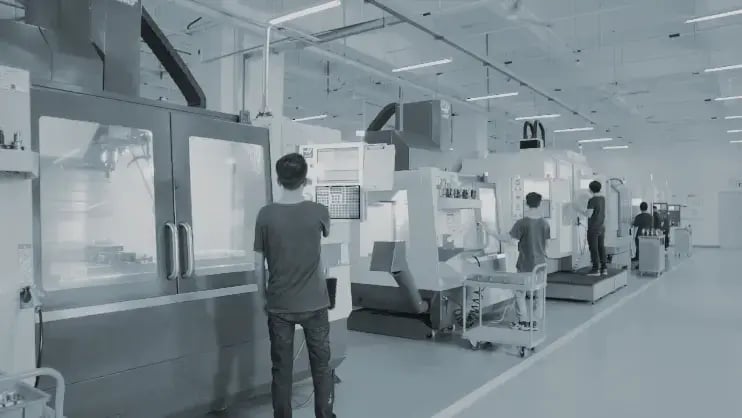
Understanding Operator Workload
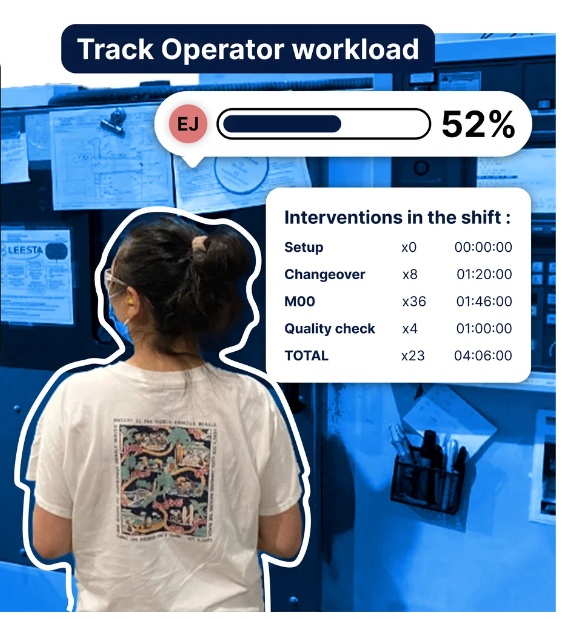
- Preventing Burnout: Overworked employees are more prone to burnout, leading to high turnover rates. Understanding their workload helps distribute tasks more evenly, ensuring no one is overwhelmed.
- Optimizing Efficiency: Analyzing the workload can reveal inefficiencies and bottlenecks in the production process. Addressing these can improve overall productivity without necessarily increasing headcount.
- Enhancing Morale: Operators who feel their workload is fair and manageable are more likely to be satisfied with their jobs, leading to higher morale and better performance.
- Accurate Labor Forecasting: Knowing the exact workload allows for better labor forecasting and scheduling, ensuring that labor resources align with production needs.
- Better Machine-to-Operator Ratio: By knowing each operator’s workload you can assign more responsibility to operators with low workload allowing them to manage multiple machines at the same time, thereby increasing productivity without increasing labour costs.
Assessing Operator Workload
1. Data Collection and Analysis
The major challenge in predicting operator workload is knowing the estimated durations of each task, which is generally not accessible. Indeed, in standard production software, such as ERP, MES, MRP or APS, only the adjustment time and the total production cycle are recorded.
During production, manual tasks which correspond to 80% of operators' working time are not recorded: time allocated for an M00 (planned stoppage in machining), time allocated for quality control, time allocated for a part change or a tool change, etc. These tasks are too micro for ERP, MES, MRP and APS, so there is no visibility in these systems whose goal is to manage higher-level operations.
In lean manufacturing practices, times can be timed manually in order to understand the standard time for each operation. Generalized at the factory level, this practice represents a Herculean task, realistically difficult if not impossible to implement and above all to maintain.
- Setup Times
- Changeover Times
- Planned Stops (M00)
- Inspection Times
2. Analyze the Data to Improve CNC Program Standard Times
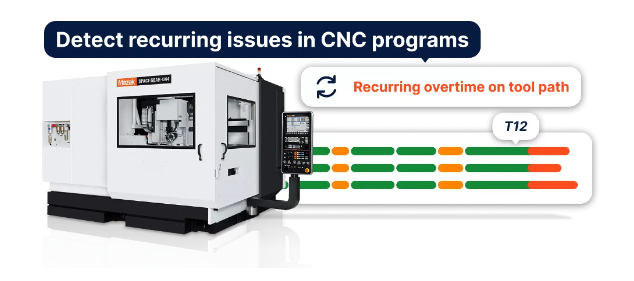
3. Plan Upcoming Work
3.1 Reassign Work to Balance Workload
Operator workload is a key indicator for making decisions on resource allocation on machines:
- If the workload is too heavy, it is desirable to reduce the number of machines managed by an operator, so as not to affect performance and introduce numerous machine stoppages.
- If the workload is too low, this helps detect opportunities where the operator could manage an additional machine, help an overloaded operator, or simply perform related tasks.
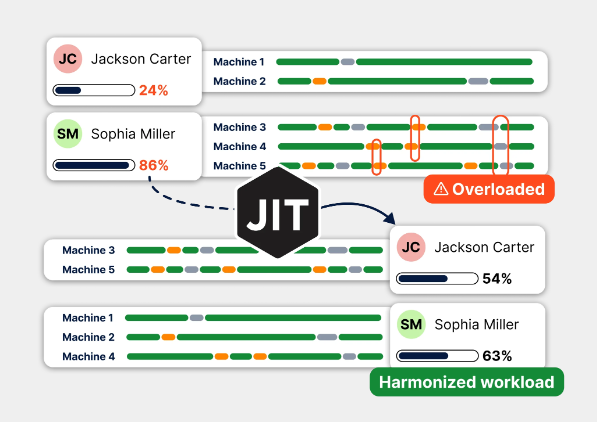
Using workload to make production scheduling decisions allows you to:
- Maximize the number of machines managed by an operator, by detecting operator underloads
- Avoid productivity issues where an operator is overworked
- Harmonize the workloads of all operators
3.2 Smart and dynamic Operator Allocation
The reality of planning is rarely the reality of production. It is therefore essential to be able to adjust the production plan, almost in real time, depending on production hazards and emergencies that arise during the day.
Connected to the machines, the JITbase workforce planning and management tool updates in real time, based on actual production progress. It is therefore possible to readjust the assignment of operators throughout the shift, to maintain the highest possible level of productivity.
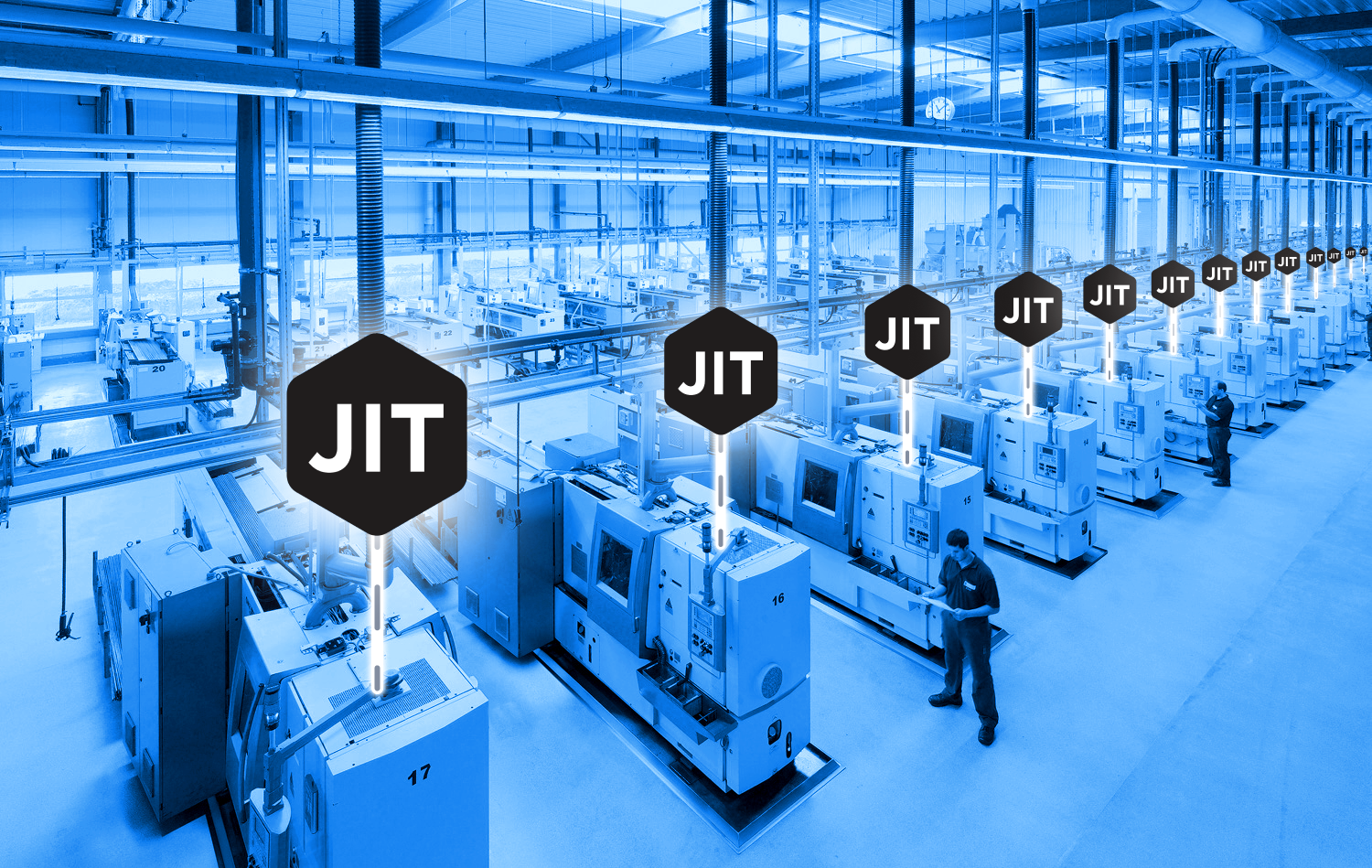
The allocation of operators to machine tools is no longer done at random, based on perceptions, but rather on a precise KPI performance indicator: the workload of the operators.
To learn more about it:
Supervisors who are generally in charge of daily planning and resource allocation on machines can now couple their expertise and experience with factual data that can guide them on essential decisions with a strong impact on the overall productivity of the plant. factory.
Conclusion
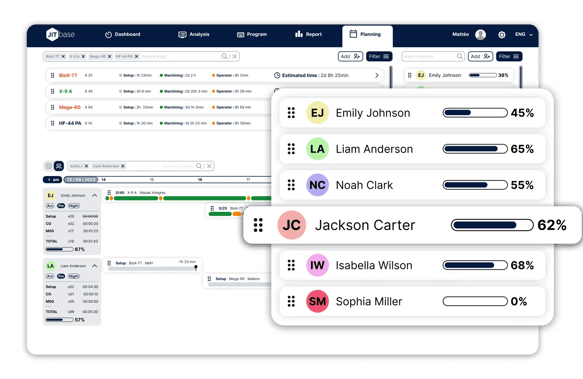
By being able to accurately calculate workloads based on the number of machines managed and the production runs on each machine, you can optimize the allocation of operators, which allows you to increase the average number of machines managed per operator, improve productivity and improve employee satisfaction.
Thanks to an improved human/machine ratio, the perceived need for additional labor is mitigated, which will reduce your challenges related to hiring and shortages of machinists and operators.